Case study
Contract and Component Manufacturing
–
Client: Confidential
Year: 2022
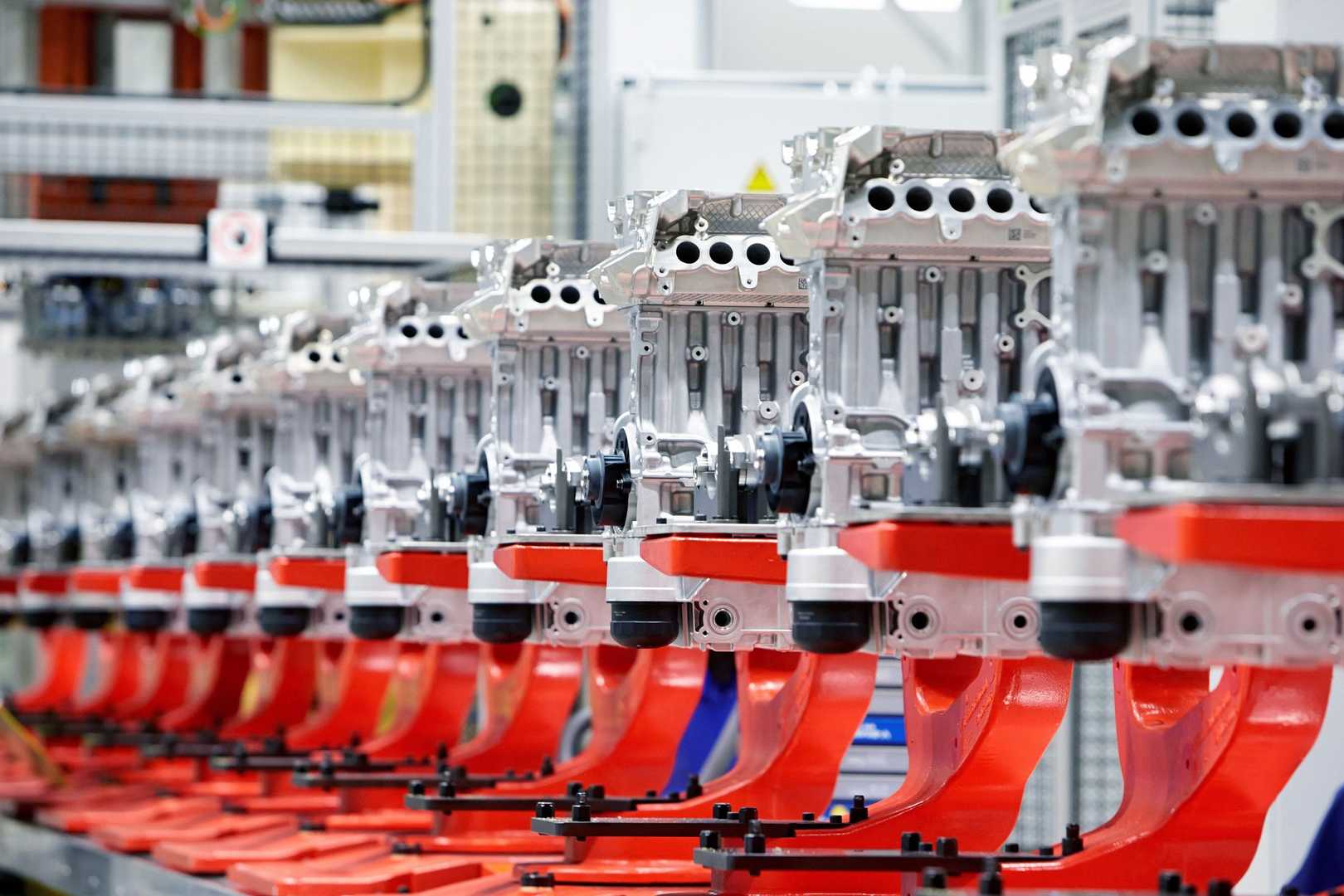
Next-generation rotorshafts for electric motors
Aurobay re-engineered the rotorshaft for an Electric Drive Unit to make it stronger, more sustainable and more efficient to produce.
The challenge
Aurobay has the expertise and infrastructure to support complex machining and manufacturing for powertrain components. So we were delighted to be approached to build to 335 000 rotorshafts a year to support assembly for production.
We are used to rigorous quality, sustainability and cost requirements. But when our product and process engineers took a look at the designs, we knew it needed adjustments to deliver.
Our solution
Our engineers proposed an alternative design to the client, with an innovative hollow shaft made using a cold-forming process. Because our tailor-made solution uses less steel, it is more sustainable and cost-effective, and tests show that the new design is stronger.
The new design means Aurobay will be able to produce 335 000 rotorshafts each year in our plant to a challenging timeline and at a competitive cost.
The rotorshafts go into production in 2024, and are set to power electric vehicles on the road from 2025.
Case studies
Next-generation 200hp-2-0l-miller-engine with astonishing fuel efficiency
Aurobay’s newest engine, the 200hp 2.0l miller designed and manufactured in-house, meets the toughest fuel-efficiency and emissions targets, with great performance.
Client Volvo Cars
Year 2021
Read More